Architecture schools are designing material innovation
Architectural design is a collective experiment. Designing Material Innovation, an outdoor exhibition at California College of the Arts (CCA), hypothesizes a future with radically different notions of material, fabrication, and design. Artifacts are interactive. Sculptures are upcycled. Prototypes are shelters and data machines at once.
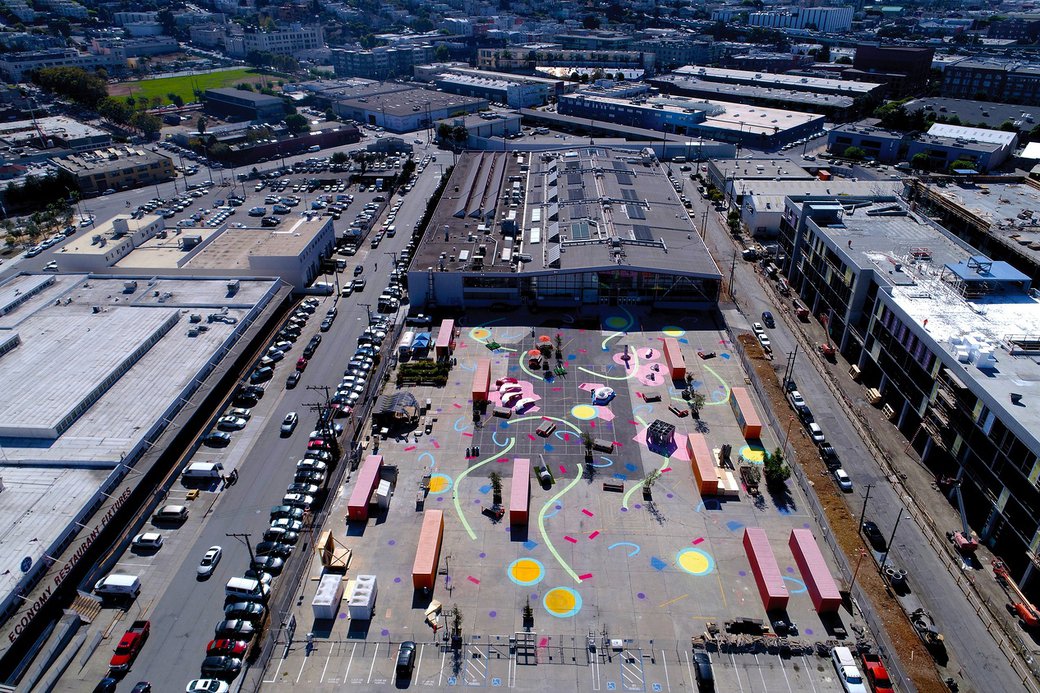
Exhibition on CCA Backlot.
The exhibition lives within an even larger (award-winning) public landscape: confetti urbanism. Colorful flecks, ribbons, and other shapes appear as though scattered across the CCA Backlot, a space students use for building and displaying art. Clark Thenhaus, the exhibition designer and artist behind confetti, is also a CCA professor and director of Endemic, an architecture firm in San Francisco that rethinks existing forms through the lenses of materiality, history, culture, and digital fabrication.
“Each emerged from collaboration,” writes Jonathan Massey, exhibition curator, in his introduction to the five prototypes.¹ Former CCA architecture dean and the current dean of architecture and urban planning at Taubman College, Massey is a proponent of design that regulates consumption and shapes social relationships. Interdisciplinary dialogue among engineers, ecologists, architects, fabricators, chemists, and architecture colleges is critical, he says, to strategic form-making.
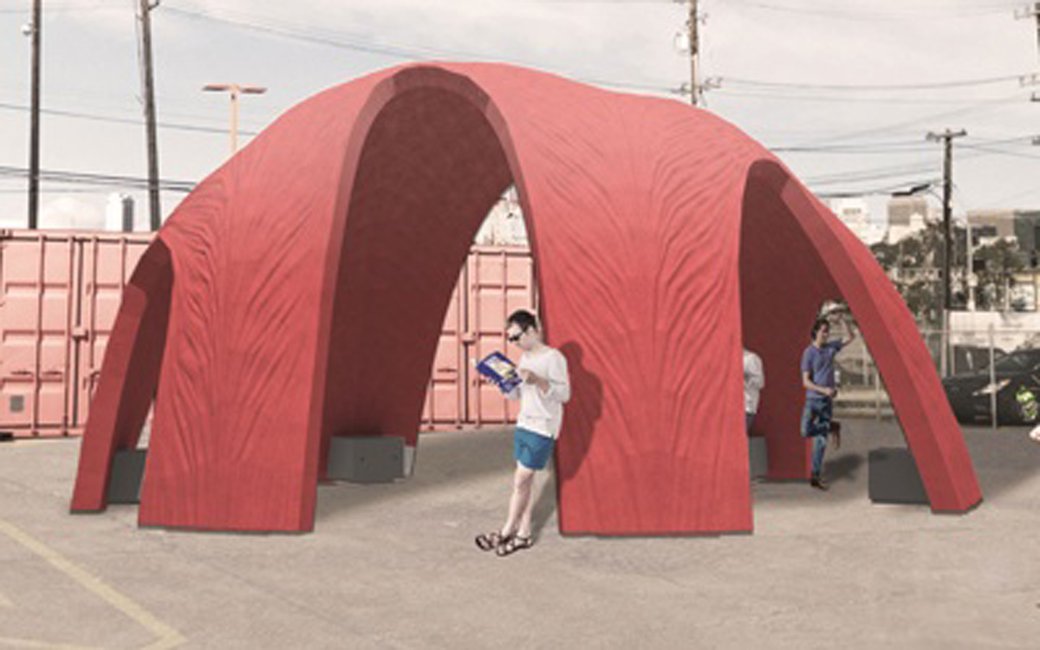
Polymorph Pavilion visualization.
Polymorph Pavilion
Polymorph, one of two pavilions in the exhibition, is an ongoing project led by the CCA Digital Craft Lab (DCL). Dedicated to “advanced research in architectural design, digital fabrication, material science, data visualization and robotics,” the DCL routinely works with industry partners on issues of sustainability.² In this case, students collaborated with a leading composites fabricator, Kreysler & Associates, to divert waste from landfills.
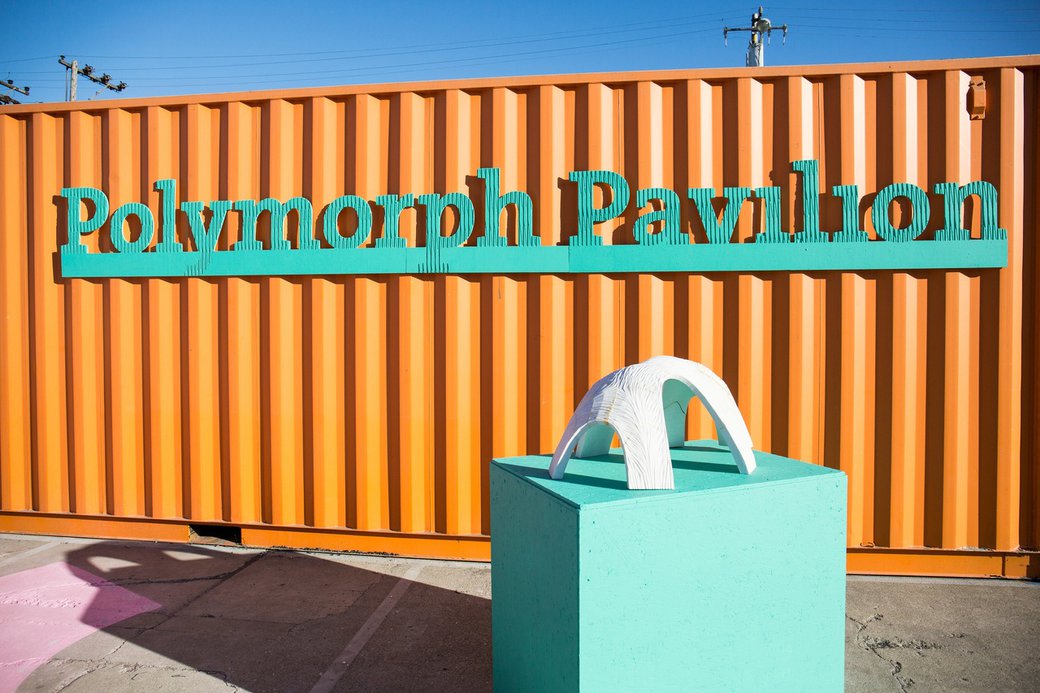
Early tabletop prototype of Polymorph Pavilion.
Upcycling & Robotic Fabrication
EPS foam is lightweight, strong, and rigid, making it ideal for a range of building applications. Its greatest strength, however, is also its greatest weakness: environmental persistence. It does not biodegrade (anytime soon).
By attaching a hot-wire cutter to a robotic arm, CCA students re-milled foam waste from Kreysler into 502 building blocks for their pavilion.³ Their approach to “second life-materiality,” which will create a sheltered space for casting concrete and plaster, invites viewers to “consider the future of building waste in a visceral way.”⁴ Polymorph is in media res—exposed, celebratory, and rife with possibility.
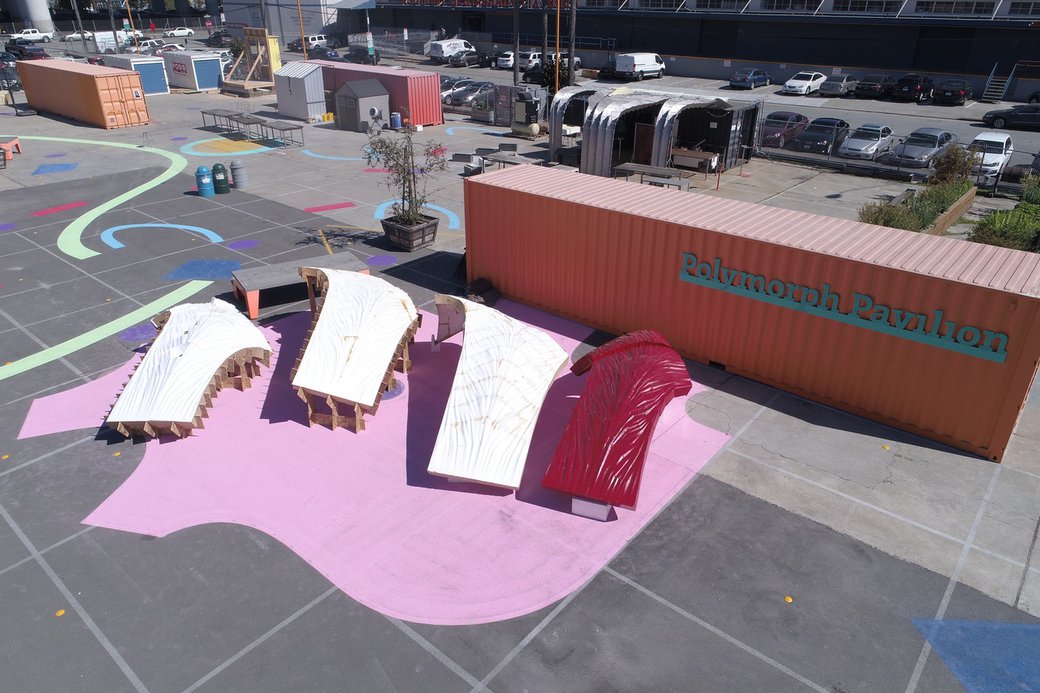
Foam building blocks and high-gloss red polyurea.
Real-World Process & Iteration
Polymorph presents students with challenges beyond the purview of most architecture degrees. They oversee every aspect of the design/build, from prototyping to supply chain management, and they collaborate with multiple generations of experts across industries.
The six-legged shell began as a series of small tabletop prototypes. Students, led by CCA professors Aaron Willette, David Shook, and Andrew Kudless (also the founder and director of MATSYS), modeled and assembled numerous forms based on their advanced studio research. Using EPS foam from Kreysler’s mold-making process, they tested various contraptions to build a full-scale prototype, improvising and iterating along the way.
To create a strong, weatherproof seal, the team coated the foam building blocks with polyurea. The resulting structural skin—in high-gloss red—forms a lightweight and sustainable composite material.⁵
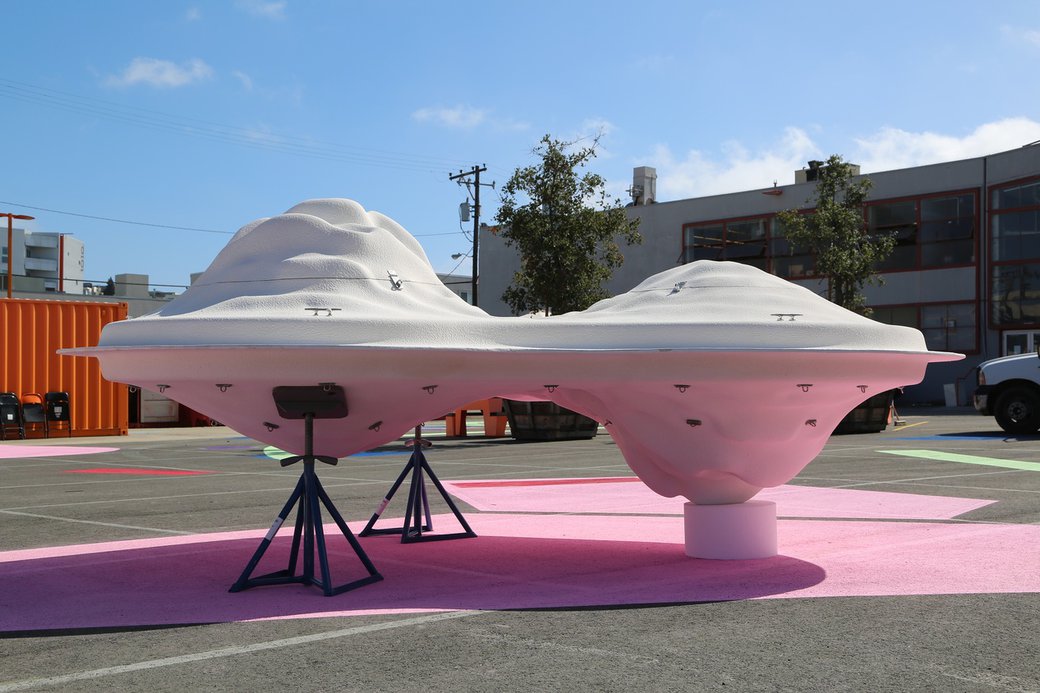
Buoyant Ecologies Float Lab on the Backlot.
Buoyant Ecologies Float Lab
The second CCA project drew inspiration from a post-Hurricane Sandy competition: Rebuild by Design. Initiated by former president Barack Obama, the competition called for innovative solutions to rising sea levels, including floating homes, liveable breakwalls, and other resilient structures. Design experts, scientists, and architecture colleges rose to the challenge with multifaceted solutions.
Buoyant Ecologies is a result of three years of applied research in the CCA Architectural Ecologies Lab. Championing collaboration and sustainable design, the team, led by architecture professors Adam Marcus, Margaret Ikeda, and Evan Jones, worked closely with Kreysler and the Benthic Lab at Moss Landing to build a structure that helps prevent coastal erosion while stabilizing the ecosystem.
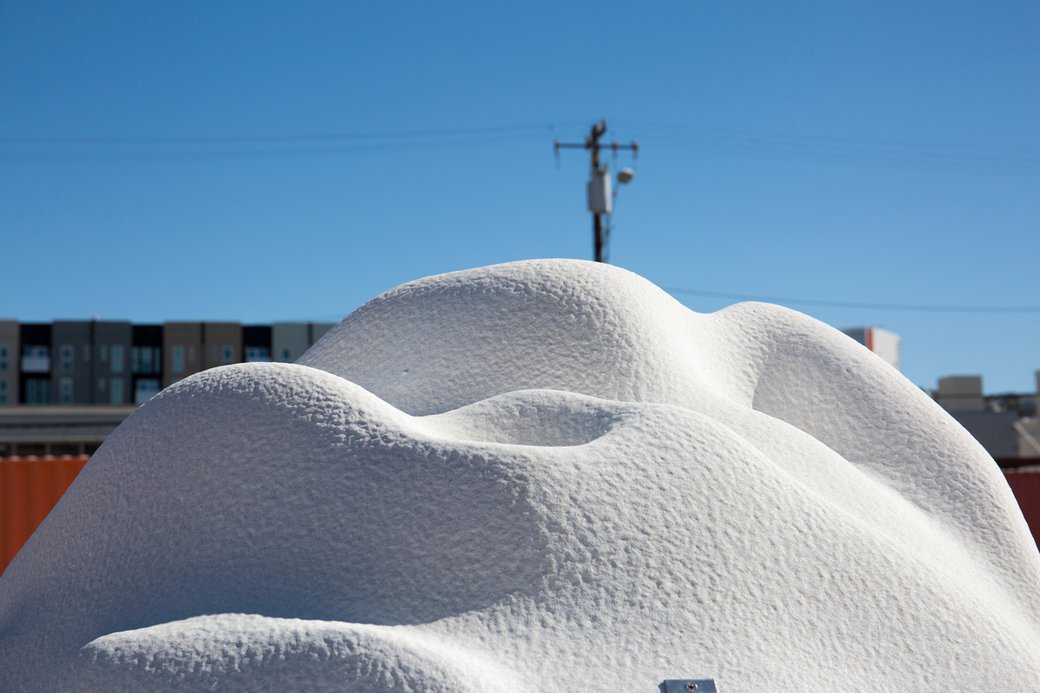
Top hull topography.
Resilient, Interdisciplinary Design
CCA joins the ranks of other architecture schools in the Bay Area to address climate issues with ethical and resilient design prototypes. The float’s two polymer hulls, which are conjoined like a clamshell, are made from a polymer composite reinforced with fiber. Developed in collaboration with Kreysler, the composite is eco-friendly and has various surface topographies.⁶
The top hull’s bumps and ridges create intertidal or terrestrial habitats by channeling rainwater into watershed pools. This floating island is simultaneously a home and research station. Varying peaks and valleys beneath the surface also provide habitats for invertebrates.
Students collaborated with the Benthic Lab to test substrate prototypes for a liveable hull. Prototypes were installed under water, giving marine ecologists a chance to monitor and measure their ecological performance over time. In partnership with the All Bay Collective, CCA will deploy Buoyant Ecologies in the San Francisco Bay in 2018. Students hope to make the case for a larger system of floating breakwaters that will help restore damaged ecologies and highlight the importance of continued conversation about sustainability.
Notes
- “Exhibition and Symposium at California College of the Arts,” Designing Material Innovation, accessed December 8, 2017,https://designingmaterialinnovation.org/
- CCA Digital Craft Lab homepage, accessed December 8, 2017, http://digitalcraft.cca.edu/
- Designing Material Innovation
- Blaine Brownell, “How Material Experimentation Can Go Well and Go Wrong,” Architect Magazine, November 16, 2017, https://www.architectmagazine.com/design/culture/how-material-experimentation-can-go-well-and-go-wrong_o
- Designing Material Innovation
- Designing Material Innovation
Find your creative community at CCA